by limor » Thu Dec 19, 2013 7:57 pm
by limor
Thu Dec 19, 2013 7:57 pm
I've been following threads around the web relating to gymball setups for quadcopters that have created this year a new market opportunity within the RC world for what they call "brushless gimbal motors".
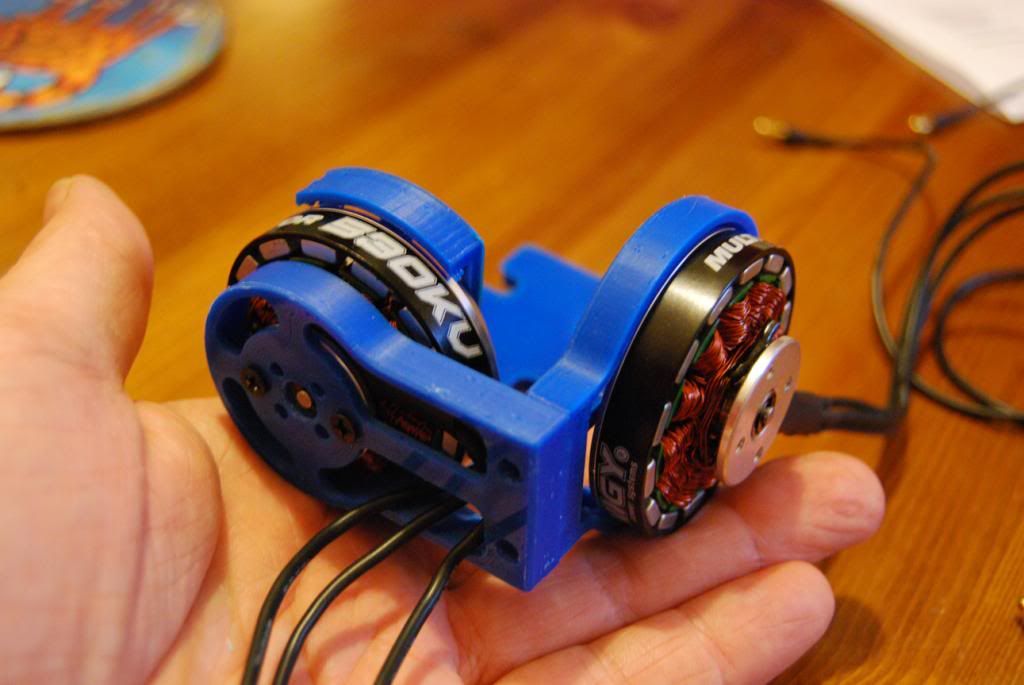
They are miniature versions of the pita motors used in electric bikes and bldc motors used in heavier electric vehicles.
I'm wondering if these can be used as robot joints.
The main advantages are that the pita motor produce quite a bit of torque without any gear reduction. This implies "direct drive" robot control which is the a better way to control robots than a servo box for some applications (no backlash, no breaking gears when hitting falling, torque control to create various compliant effects etc.)
I've seen ones decently priced motors producing 5.5kg-cm and expensive heavy ones producing 10kg-cm. They are designed to stabilize and fight in realtime against serious vibrations driving a payload of 1.5kg cameras.
As with anything in the RC hobby, there are no exposed useful measurements and tolerances. Most values exposed are not very useful for engineering purpose.
To actuate walking robot legs, the 5.5kg-cm can be multiplied by using a wire or belt and pulley ratio of 1 to X to create (a) decent amount of torque and (b) retain the no-backlash, direct-drive feature (c) get a nicer biologically inspired structure by hiding the motor in some other part of the body rather than having the pita motor in the knee.
I'd love to hear opinions or experience with these motors from a robotic perspective.
I've been following threads around the web relating to gymball setups for quadcopters that have created this year a new market opportunity within the RC world for what they call "brushless gimbal motors".
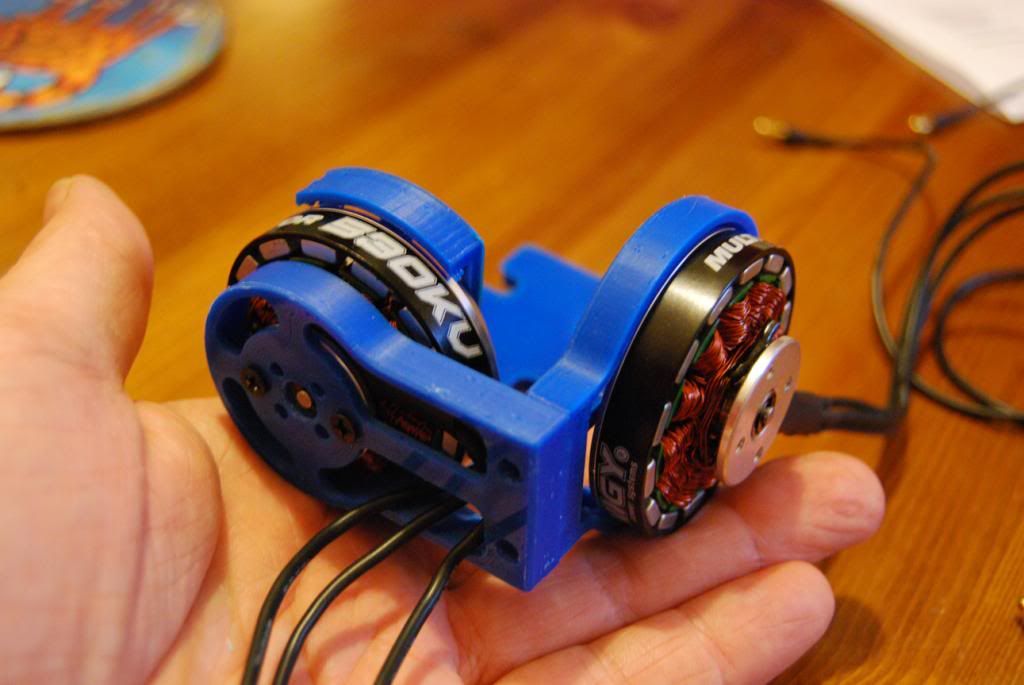
They are miniature versions of the pita motors used in electric bikes and bldc motors used in heavier electric vehicles.
I'm wondering if these can be used as robot joints.
The main advantages are that the pita motor produce quite a bit of torque without any gear reduction. This implies "direct drive" robot control which is the a better way to control robots than a servo box for some applications (no backlash, no breaking gears when hitting falling, torque control to create various compliant effects etc.)
I've seen ones decently priced motors producing 5.5kg-cm and expensive heavy ones producing 10kg-cm. They are designed to stabilize and fight in realtime against serious vibrations driving a payload of 1.5kg cameras.
As with anything in the RC hobby, there are no exposed useful measurements and tolerances. Most values exposed are not very useful for engineering purpose.
To actuate walking robot legs, the 5.5kg-cm can be multiplied by using a wire or belt and pulley ratio of 1 to X to create (a) decent amount of torque and (b) retain the no-backlash, direct-drive feature (c) get a nicer biologically inspired structure by hiding the motor in some other part of the body rather than having the pita motor in the knee.
I'd love to hear opinions or experience with these motors from a robotic perspective.