by TiagoM » Fri Feb 15, 2013 12:39 pm
by TiagoM
Fri Feb 15, 2013 12:39 pm
Howdy!
Here is the build process of the sensor board for the hand of our 1m humanoid robot.
It's a 24 FSR 8 Servo board based on the Arduino Leonardo (the Atmega32u4 chip).
The board has 5 8-input 10bit ADCs capable of doing 200ksps to read the 24 sensors, servo position and servo current.
Anyway, without delay here are the pictures:
Securing the board with Kapton tape
Leveling with other boards of the same hight
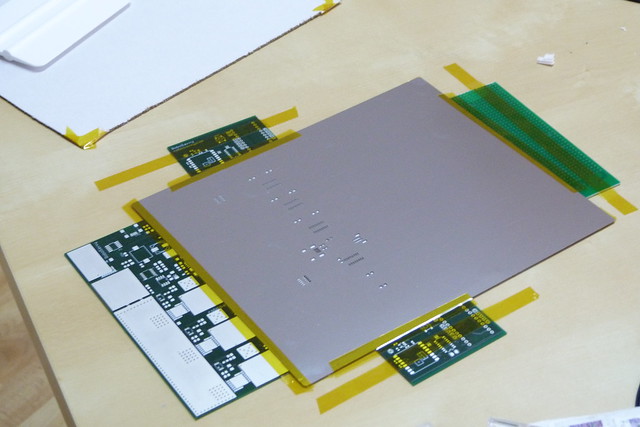
- Securing the stencil on top
Applying the paste with the Makerbot's squeegee
Solder paste applied
Placing all the components, one by one
Bottom part done
Raiser tool printed on the Replicator 2. Because it's a dual-sided board we had to raise it in order to level it.
Again, leveling with other boards
Board in the oven
Programming the board, Macgyver style
Ta-da! Board done.
And that's all folks.
I'm now programming and testing it but so far so good!
Cya
Howdy!
Here is the build process of the sensor board for the hand of our 1m humanoid robot.
It's a 24 FSR 8 Servo board based on the Arduino Leonardo (the Atmega32u4 chip).
The board has 5 8-input 10bit ADCs capable of doing 200ksps to read the 24 sensors, servo position and servo current.
Anyway, without delay here are the pictures:
Securing the board with Kapton tape
Leveling with other boards of the same hight
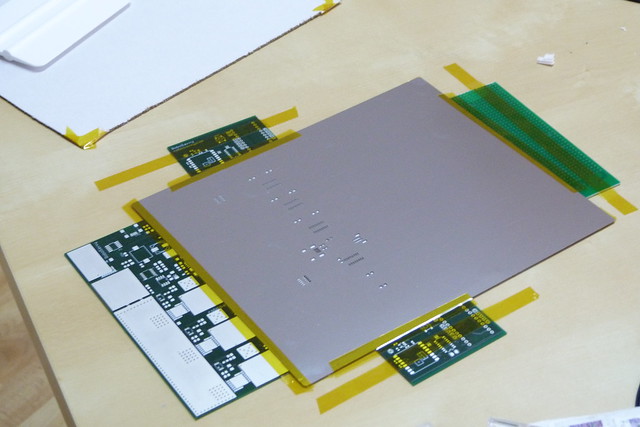
- Securing the stencil on top
Applying the paste with the Makerbot's squeegee
Solder paste applied
Placing all the components, one by one
Bottom part done
Raiser tool printed on the Replicator 2. Because it's a dual-sided board we had to raise it in order to level it.
Again, leveling with other boards
Board in the oven
Programming the board, Macgyver style
Ta-da! Board done.
And that's all folks.
I'm now programming and testing it but so far so good!
Cya